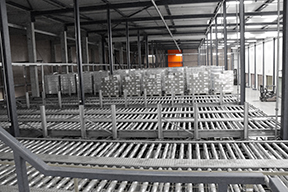
Smooth operation in automated cold store
In 2013 Germany's first, largest and highest fully automated cold store was built by KLM Logistic in the city of Rheine in northwestern Germany. NewCold, that is the subsidiary to KLM Logistic, supplied the racking systems for the cold store. A total of 68,000 pallets in the warehouse holds frozen products such as ready-made-meals, ice cream, cakes and fish products. KLM distributes the products to retailers in Germany, Benelux, Southern Europe and England.
Traditional problems in cold stores
The large number of loadings every day means many openings of the doors to the outside. This allows for moist and warm air to enter into the lock and further into the cold store where it will cause snow, frost and ice formations. Ice built up on the packed goods can disturb reading of barcodes and softening of packing materials. Ice and frost on walls, ceilings and floors is a well known problem that entails not only costly man hours for removal and defrosting, but also causes dangerous conditions for fork lift drivers.
The efficiency of freezing equipment incl. evaporators will be reduced due to ice built-ups and time comsuming defrosting cycles are needed to remove the ice.
The solution at KLM
KLM was aware that the fully automated picking and loading system in the huge cold store that operates at a temperature of -24° C, could not function without a solution that would effectively control the humidity.
In the air locks at all loading docks KLM decided to install Munters desiccant dehumidifiers type MLT800 that are running in continuous operation.
Dehumidification goes to the root of the problem by removing moisture from the warmer, humid outside air that enters the loading dock. By reducing the humidity in the air in the loading docks, the water content in the air that penetrates further into the cold store is so low that condensation of the air is prevented. Thereby the formation of snow, ice and frost is no longer a risk.
KLM's automated cold store would not be able to operate without using dehumidification. The many sensors and conveyor bands for the automatic picking and loading of goods would be disturbed by ice build-ups, so the humidity has to be kept low and constant around the year.
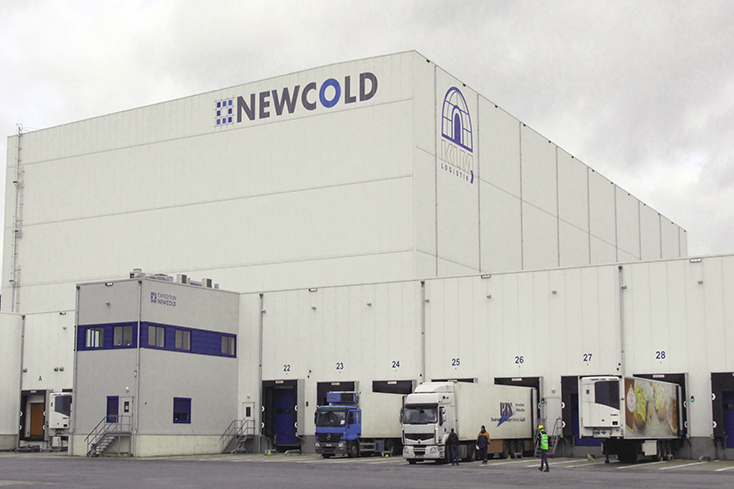
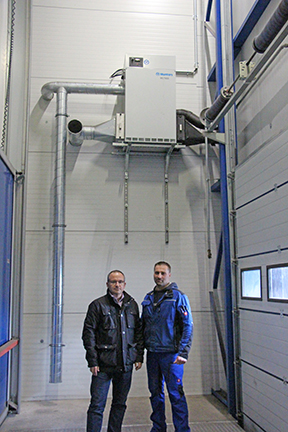