丹麦一巧克力糖果工厂靠工业转轮除湿机节省大量干燥时间和能耗
Carletti is a Danish chocolate and candy producer that started in 1918 as a small wholesale company.
Today, Carletti produces and sells a wide variety of chocolate and candy products through retailers for private consumers – primarily in Denmark and Northern Europe.
As a modern company with a strong focus on competitiveness, energy savings are a strategic goal. Carletti has recently worked on four major energy-saving projects together with Ole Jacobsen from the Danish Energy Consultancy. Two of these projects concerned the installation of dehumidification of process air in coating processes and converting oil burner into LPG-burner on their steam boiler.
Carletti used to have an older ventilation system to supply hot air to processes where there was a need for dry air to color, polish and dry products.
Carletti has now invested in four desiccant dehumidifiers from Munters and has thus been able to reduce energy consumption by up to 50 %. The process itself is a slightly more expensive process, but in return, the production capacity increased by shortening the drying process from 19 to 12 hours for a batch of 4,500 kg chocolate lenses.
Steam for rotor regeneration
Munters dehumidifiers are an example of the positive effects that can be derived by switching to more energy efficient solutions.
These two energy projects (converting oil burner to LPG gas burner and installation of dehumidifiers) are closely linked, as a part of the steam from the gas boilers is used to heat the air that removes the absorbed moisture from the desiccant wheel (rotor) in the dehumidifiers.
The fact that gas is cheaper than oil, has reduced CO2 emissions and allows for stepless control of the energy supply - unlike the oil boiler which only had a high and low setting.
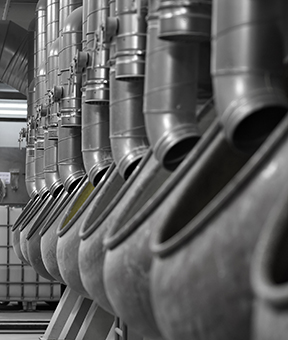
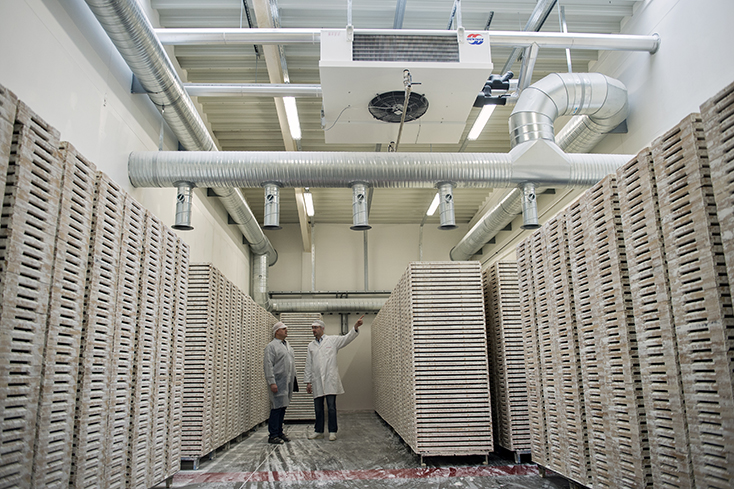